Design for the Environment/Institutional Cogeneration
This page is part of the Design for the Environment course
As Toronto Medical Officer of Health Dr. David McKeown said “Air pollution is responsible for 1,700 premature deaths and 6,000 hospital admissions in Toronto each year” [1]. Moreover, a significant portion of these impacts is due merely to the production of electricity and heat. Therefore, it is vital to understand these environmental issues and to develop more proactive designs in order to solve them. This article analyzes the environmental, societal, functional and economic impacts of three alternatives for providing heat and electricity to the University of Toronto (institutional cogeneration). The baseline alternative is for the university to purchase electricity from Toronto Hydro and produce heat by means of the already existing natural gas boilers. Additionally, two more environmentally friendly alternatives are considered, they are: the utilization of Solid Oxide Fuel Cells (SOFC) or to retrofit the existing boiler system for cogeneration by adding a steam turbine and generator to produce electricity. As a common function, each of the alternatives considered must provide 985 000 MMBTU of steam and 188 000 000 kWh of electricity per year to the university [2]. This analysis considers the impacts of the various processes along with the acquisition of the fuels and utilities. Furthermore, it looks at the impacts of transportation of the fuels; as well as recycling of the utilities. The optimum goal of this analysis is to recommend to the client, the University of Toronto, the best option to implement among the ones analyzed.
Painter: Sir Edmund Walker Year: 1859 Source URL: http://www.fineart.utoronto.ca/canarch/ontario/toronto/uc.html]]
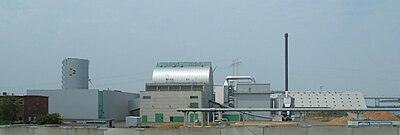

Project Information
editSection 1 Group A2
Maby Boado Amador (boadoama)
Michael Bosompra (bosompra)
Joshua Sissons (sissonsj)
Michael Wong (wongmi18)
Highlights and Recomendations
editThe main functional similarity between the three alternatives is the use of natural gas as the fuel for the generation of heat and electricity. The main difference is the process by which each of the alternatives accomplishes the required functions. Comparing the performance of the three alternatives, it is apparent that Alternative 1 has an advantage over the Baseline and Alternative 2. The whole plant efficiency of Alternative 2 is approximately 60%, whereas with just boilers (Baseline alternative), the efficiency would be around 40% [3]. Furthermore, the efficiency of the fuel within the solid oxide cell when only generating electricity is 50% [4]. A thermal to electric ratio of one was assumed, [5] implying 100% efficiency. However, this is not a valid assumption, since heat will inevitably be lost in the process. Therefore, an estimated efficiency of this process would be 70% [6]. Another important issue considered is the space required for the power plants. Alternative 1 would require the construction of a large facility since it needs 44000m2 of land for the placement of the stacks. See details below.
Figure 1 serves as a quick visual aid in comparing the three alternatives based on their Streamlined LCA. As it can be seen, the environmental impacts of the three alternatives are similar in the resource provisioning stage. The reason for this similarity is that they all use natural gas as the primary fuel. During the process implementation stage Alternative 1 ranked the highest, meanwhile the Baseline and Alternative 2 were given similar, lower scorings. The main reason for this is that the production and installation of the fuel cells require simple manufacturing techniques using fairly inexpensive materials, while the other two require the extensive use of high strength steel and other virgin metals [7]. Furthermore, Figure 1 shows that Alternative 2 scored close to Alternative 1 for the primary process operation. The reason for this is intrinsic of an ideal cogeneration system. By using the byproduct of one process, in this case heat, as the input product of a subsequent process the total energy used can be reduced considerably. Alternative 1 has the advantage over the Baseline and Alternative 2 in terms of gaseous emissions. Carbon dioxide and methane are reduced by approximately 75%, and the NOx, SOx, CO, and particulate matter emissions are almost negligible [8]. Complementary processes operation follows the same trend that the primary process one and as so, Alternative 1 has the highest score of the three. The three alternatives scored similarly for the end-of-life stage. The reason for this is the similarity in the materials used in the systems, mainly metals, which are mostly recyclable. In addition, since the fuel burned is natural gas, all pipes, vessels, tanks, etc are fairly clean. Based on the Streamlined Life Cycle Analysis the usage of Solid Oxide Fuel Cells has the least environmental impacts with a matrix total of 70, while the Baseline and Alternative 2 had totals of 53.5 and 62, respectively. See details below.
The EIO-LCA model is another means of estimating environmental impacts by dividing the process into different sectors and determining the burden releases per unit of economic activity. Figure 2 and Figure 3 serve as quick visual aids in comparing the three alternatives based on their EIO-LCA model results. Totals regarding Global Warming Potential(GWP), SO2, CO, NOx, VOC, PM10 and toxic releases are compared among the alternatives. Alternative 2 seems to be the worst polluter regarding Global Warming Potential emissions (7,240,884 MTCO2E). The largest portion of this total comes from the process of burning and distributing natural gas, which releases large amounts of CO2 into the environment. On the other hand, Alternative 1 produces far less GWP than the other two alternatives, which explains why Solid Oxide Fuel Cells are being researched so thoroughly, but releases the most toxic releases out of the three alternatives. The extraction of raw materials accounts for almost all of the toxic releases, due to the large amounts of residue from mining the metals the Solid Oxide Cells are made of. The Baseline Alternative releases the most conventional pollutants. The largest contributor to this result is the generation and distribution of electricity. Once again, Alternative 1 has the least emissions. For this alternative, most of the pollutants come from the natural gas processes; however, the PM10 are split between the natural gas processes and the extraction of raw materials of the system. Overall Alternative 1 seems to be the more environmentally friendly and this agrees with the Streamlined Life Cycle Analysis. However, the Baseline and Alternative 2 seem to be similar, since Alternative 2 has higher GWP and the Baseline alternative has higher toxic releases and conventional pollutants. See details below.
Figure 4 summarizes the economic analysis of the three alternatives and it divides the total cost into its respective areas of occurrence. Reoccurring costs for the Baseline Alternative are the purchasing of the electricity from Ontario Power Generatin(OPG), for Alternative 1 the acquisition of the new fuel cells every three years and for Alternative 2 are minor things such as control system upgrades. This reoccurring cost is where most of the cost of the Baseline alternative comes from (approximately $ 171 million), since this alternative is already implemented and has no capital cost. Natural gas needs to be purchased by every alternative but by different amounts. The Baseline alternative uses much less fuel than the other two, approximately 40% less than Alternative 1, since it only uses it to produce heat. Furthermore, Alternative 1 consumes much less fuel than Alternative 2 in the use phase, approximately 60% less, since it does not have a turbine. It is evident now that the bulk of the cost of each alternative come from different sources, the Baseline’s comes from the purchase of electricity ($ 171.91 million), Alternative 1’s comes from the implementation of the process ($ 227.88 million) and Alternative 2’s comes from the larger amount of fuel consumption ($ 246.82 million). Overall Alternative 1 is the pricest. See details below.
Alternative 1 is the one that has the least negative effect to the community surrounding the University, while the Baseline and Alternative 2 would be ranked equally. The main advantages of the Solid Oxide Fuel Cell cogeneration system are the low noise and emissions levels of the process. The lower greenhouse gas and toxic release emissions would improve the air quality of the University’s community and would contribute to maintain the aesthetics of the city of Toronto by reducing smog and odours. These lower emissions would also improve the health of the population since the prolonged exposure to increased NOx levels could affect people with asthma or bronchitis. See details below.
Based on the above shown decision-making matrix (Table 1) a Solid Oxide Fuel Cell power plant would be the best option for the University of Toronto. However, other issues, primarily the availability and high cost of this alternative, must be considered. Nowadays, this technology is only generating 250 MW per year and U of T requires 476 602 MW. Furthermore, the cost for producing energy with this technology is approximately $850/kW [9], which results in around $ 440.18 million over its entire life. Just over half of this total amount would be spent during the implementation of the process ($ 227.88 million). However, what make this alternative feasible are the fast improvements on its technology and efficiency. It is expected that by 2010 it will break the barrier of $400/kW [10]. On the other hand, the University of Toronto’s annual budget shows an operating surplus average of $20 million per year [11]. This outstanding total could be used to implement this technology in a span of 10 years after this alternative becomes economically viable. It is important to highlight that Alternative 2 is better than the Baseline Alternative since it has higher efficiency (60% and 40% respectively) and according to the SLCA less environmental impacts. Furthermore, the University would not be dependent on external parties for the acquisition of electricity and would not be influenced by market price fluctuations. Alternative 2 also has some advantages with respect to Alternative 1. For instance, Alternative 2 could be implemented in the same boiler house that the University already owns, rather than needing another building, which saves money and time. However, it is not advisable to switch to Alternative 2 just yet since Alternative 1 is predicted to be commercially viable in less than 5 years.
After careful analysis it was decided that the final recommendation for the power generation of the University of Toronto is to maintain its current technology (Baseline Alternative) and to implement gradually the Solid Oxide Fuel Cell power technology (Alternative 1) as it becomes commercially available and economically suitable.
Details of the Functional Analysis
editBaseline Alternative
editFunctionally, the baseline consists of two parts; firstly, purchasing electricity from Toronto Hydro, and secondly heating the university via a boiler system like the one shown in the adjacent diagram.
Alternative 1
editThe Solid Oxide Fuel Cell (SOFC) utilizes cathodes, electrolytes, anodes, and interconnects to electrons. The Solid Oxide Fuel Cell system consists of three main sectors, the balance of plant (heater, control system, etc), the balance of stack (seals, electrical, pressure vessel, etc), and the stack structure (fuel cell). The advantages of the system include waste heat, various fuel compatibility, no moving parts, and lowered emissions. However, the system requires a slow start up time and is not yet commercially viable. The fuel cells are to be replaced every three years due to degradation. The thermal to electric ratio of the system is assumed to be one, so the heat energy generated will be equal to the electric energy. Natural gas will be used in the analysis to generate 813 322 MMBTU of electricity at 50% efficiency.
Alternative 2
editAlternative 2 involves retrofitting the existing boiler system to include a 35 MW gas turbine-generator linked to four boilers. AC power is generated simultaneously with steam as hot exhaust gases from the gas turbine are collected in a duct burner attached to a boiler. Oxygen-rich gas allows additional fuel gas to be burnt in the boilers, thereby increasing the steam capacity and increasing the overall efficiency of the system. To further increase the plant’s efficiency, heat exchangers, economizers and a percotherm are used in the heat recovery system. The steam created flows to most of the buildings on the St. George Campus where it is used in radiators, chillers, etc [12]. The main advantage of this system is that it utilizes the existing boiler house on campus and is able to contribute to the full electricity load. Disadvantages of the system are that it requires a lot of natural gas and contributes to direct emissions on campus. The following figures outline the overall process.
Details of the Streamlined Life Cycle Assessment
editBaseline Alternative
editThe lowest scores over all were during the primary process life stage and specifically due to the energy use during this stage. The reason for this is two fold, firstly, the baseline boilers do not have any cogeneration implemented. Thus the heat from the boilers escapes unused. Secondly, the relative size of the primary process equipment used to generate electricity necessitated the low score. The fact that energy use turned out to be the most critical environmental stressor is not surprising considering that the fuels are all virgin materials, and that the generation processes and equipment are large in scale.
Alternative 1
editThe resource provisioning involves the extraction of natural gas, metals, plastics, and other materials required for the system. The extraction of the metals will result in solid residues, acid mine drainage and other toxic liquid residues, and greenhouse gases [13]. Energy is also required for all resource provisioning processes. The implementation of the system will require lots of energy for manufacturing. The carbon dioxide and methane emissions from the primary process are reduced to 75% of emissions from the national grid and heat from a natural gas turbine, while NOx, SOx, CO, and PM10 are almost negligible. The majority of the machinery is made from steel, and therefore can be recycled, but the fuel cells are made of a complex composition of metals, which cannot be reused. The plastics and other instruments that cannot be reused or recycled will be sent to landfills.
Alternative 2
editNatural gas is the resource used in alternative 2, therefore the resource provisioning stage is the same as the baseline. Implementing the large gas turbine on the fourth floor of the boiler house is an energy intensive task; high strength steel in the gear box and the turbine are needed for reliable operation which means virgin metals are needed. The primary and complementary process operations have relatively smaller environmental impacts than the other life stages due to the use of reheatable water. The process is designed to recover the water sent out to buildings around campus by re-circulating the return water through the heat recovery system or boilers [14]. The plant uses minimal energy because the hot exhaust gas from the turbine is high in oxygen content and allows additional fuel gas to be burnt by using duct burners. At the end-of-life of the boilers and turbine, dismantling is an energy intensive process since the boilers are approximately 3 ½ stories high and are not modular. However, most of the steel is salvageable since natural gas is clean burning unlike liquid fuel.
Details of the Economic Input Output Life Cycle Assessment
editBaseline Alternative
editThe flow charts illustrate the various stages and how they fit together to form the over all process. At each stage there were associated environmental impacts which are outlined in detail in the table below. It is important to note that the rows titled “Total” are the total emissions at the end of the 30 year life, and not simply the addition of all emissions.
Ontario Power Generation spends $112 million per month on fuels for their generation stations; the three types include hydro, fossil fuel, and nuclear powered[15]. By knowing how much electricity they produce each month and how much the university consumes it is estimated that the university is responsible for $1.9 million per year. Therefore, to model the electricity acquisition process $1.9 million was split up into various mining and refining sectors to simulate the acquisition and processing of fossil fuels and uranium. Following this, the money was inputted into appropriate transportation sectors to simulate transporting the fuels from the mining sites to the power plants. It should be noted that in the case of hydro power plants the water does not need to be transported from a “mining site” but it still needs to be transported from a holding area through the plant. After transportation, the total sum was inputted into the power generation and distribution sector to finish off the process. Lastly, it is important to note that there is no “end of life” stage for this process.
Based upon the amount of steam the univeristy uses each year and the price of natural gas in January of 2008 [16], it is estimated that the university is responsible for the equivalent of $5.1 million in 1997. This dollar amount was inputted into oil and gas extraction sectors then into various distribution sectors. Following that a process model had to be constructed to accurately model the effects of burning natural gas; and lastly, using the 1-3-9 manufacturing rule recycling values were estimated.
Alternative 1
editThe amount of natural gas required is equivalent to 1.63 million MMBTU, and the extraction and distribution of the natural gas have to be considered. The material extraction and manufacturing of the balance of plant (machinery), balance of stack (seals, electrical), and the stack structure (cathodes, electrolytes, anodes, and interconnects). The amount of resources required was estimated using the 1-3-9 method. The global warming percentage during the use phase compared to electrical energy obtained from the grid and heat from a gas boiler is approximately 75%, and the NOx, SOx, CO, and PM10 emissions are almost negligible. At the disposal phase, the steel is to be recycled and all other components are put into landfills. Therefore, the emissions related to the mining of iron (which is used to make steel), is subtracted from the total (included as a credit). The table below illustrates the environmental effects of a Solid Oxide Fuel Cell Power Generation system over 30 years. The majority of the greenhouse gas potential comes from the generation of electricity and heat, however, the extraction and distribution of natural gas also accounts for a large portion. The conventional air pollutants, with the exception of PM10, originate mostly from the natural gas processes. The inhalable particles are split between the natural gas processes and the extraction of raw materials of the system. The extraction of raw materials also accounts for almost all of the toxic releases, due to the large amounts of residue from mining metals. The manufacturing phase, in relation to the other phases, does not have a big influence on the environment when compared to the other phases such as natural gas processes and the extraction of raw materials. The disposal phase, which involves the recycling of steel, actually reduces the sulphur dioxide, NOx, and inhalable particles.
Alternative 2
editThe total required energy per year for new plant is the summation of the turbine process, the boiler process and the fuel gas used in the gas compressor, respectively: 3,012,000 + 819,000 + 25,000 = 3,856,000 MMBTU/year [14]. The cost of natural gas per year in the 1997 amount is then $20.16 million. This amount was put into the EIO-LCA model under oil and gas extraction sector to account for the process of acquiring natural gas from the ground, as well as natural gas distribution sector, which includes the transmitting and distribution of natural gas to final customers. The use phase was done conventionally with the help of an emissions table from Natural Gas Issues and Trends which gave pollutants in lb/billion Btu which was converted to MT/MMBtu and then multiplied by the amount of required energy [17]. Emissions from the manufacturing of the primary process (turbine and generator) and complementary (heat exchangers and percotherm) were estimated using a cited $50 million capital cost for the whole system implementation. 75% of that cost was assumed to be from the primary process equipment manufacturing, 23% from the complementary and 2% from shipping, packaging and labour. The EIO-LCA sectors used for these percentages were: Turbine and turbine generator set units manufacturing, Wiring Device Manufacturing, Air and Gas Compressor Manufacturing and Heating Equipment, Except Warm Air Furnaces. End-of-life emissions are minimal: wiring and circuitry would be discarded to landfill but a credit would be afforded for recycled steel of about $16.38 million meaning the amount of pollutants correlating to this amount in the iron ore mining sector can be subtracted from the total pollutant tally.
Details of the Economic Analysis
editBaseline Alternative
editAdditionally to the direct costs outlined in the table, there would be indirect costs which would include taxes, depreciation of equipment, office supplies and insurance. Basically, indirect costs encompass espenses that are very necessary but do not contribute directly to the manufacture of the end product.
Alternative 1
editThe direct cost includes the facility, fuel, personnel, and maintenance of the system. The capital cost for the Solid Oxide Fuel Cell power generation system is the cost of the Balance of Plant, the Balance of Stack, and the Fuel Cell Stack. The recurring costs consist of the annual cost of natural gas, personnel, and maintenance, and the replacement of the fuel cell stack.
The indirect costs associated include insurance, taxes, depreciation, and utilities. The high operating temperatures and heavy machinery will induce safety hazards, which would increase the insurance rates. The power generation facility is used for generation within the university and would not result in any significant profits, however, taxes for the purchasing of parts and land taxes will have to be paid. All the components of the plant have a finite life span, so there will depreciation of the value of the parts. Lastly, because the system generates its own power and heat, the only utility fee that will have to be considered is water consumption.
Alternative 2
editTable 10: Balance sheet showing the direct costs resulting from Alternative 2
An advantage to this system is that the boilers are considered a sunken cost at this point as they currently exist and a decision on implementation no longer requires analyzing them except when recycling. Fuel gas is the cost of natural gas per year as calculated in the EIO-LCA section. Labour costs include the operator and engineer salaries with an estimated 3 operators required at $45,000/year and 2 engineers at $90,000/year. Lastly, a recycling deposit was subtracted from the total cost as credit to the plant. For scrap steel there is $49.4 per tonne recoverable; in 2008 this value is $64.17/tonne and with 348 m3 estimated volume of recoverable steel a recycling deposit of $175,505 results [18]. The resulting total cost of operating the cogen system over the next 30 years is equivalent to paying $303,467,000 today.
The indirect costs associated with this alternative also include insurance, taxes, depreciation, and utilities as the previous alternatives. Insurance would be slightly higher for this alternative than the baseline because of the turbine-generator. It is known that no taxes are paid since the plant is on university land [19]. After 30 years, the depreciation would take the salvage value to zero if it followed the linear curve. The same held true for boilers. Therefore, salvage value did not play a role in the total cost. Utilities such as electricity for lighting and water for boilers report an annual amount of $ 7.2 millions, which in present worth would be $ 0.72 million.
Details of the Societal Analysis
editBaseline Alternative
editThe major societal concern related to the baseline is the emissions out of the stack. The clouds of grey entering into the atmosphere are not aesthetically pleasing and more importantly could damage the university’s reputation. The university is perceived to be home to some of the brightest minds, and newest technologies in the country; with such a large emphasis being placed on “green” alternatives and smaller ecological footprints the billowing stacks could symbolize apathy on the part of the university. Without considering the entire life cycle it would appear that the university elected for the cheapest alternative without consideration for their neighbours or the environment; a conclusion that could have negative long term effects.
Alternative 1
editThe size of the facility would be quite large, so an appropriate land space would have to be found. There is not much land around the campus that could be used for construction, and existing buildings all serve their own purpose, so to sacrifice their land space would not be a solution. However, because the noise and vibrations emitted from the system are minimized due to lack of moving parts, such as turbines, the facility can be placed in any area without causing too much disturbance. The lower greenhouse gas and toxic release emissions, as discussed in previous sections, would improve the air quality around the campus, and improve aesthetics by reducing smog and odours.
Alternative 2
editNoise and pollution are the main societal effects this cogeneration process will have on the people around the university. Given the right conditions (wind direction and turbine rpm) noise generated from the boiler house assuming the windows are open can reach 95 dB maximum. Constant exposure to this amount can damage hearing [20] [21]. For pollution, direct burning of natural gas emits 441 kg of NOx and 192 kg of carbon monoxide per day based on the values from the EIO-LCA. NOx is what creates the smog in the atmosphere and people with asthma or bronchitis have increased sensitivity when exposed to it [22]. Increased CO means decrease of oxygenated blood, which impairs learning ability and visual perception.
See also
editReferences
edit- ↑ “New index measures health risk from air pollution in Toronto” News release, [online article] (July 9, 2007), available at: <www.toronto.ca>
- ↑ “The University of Toronto Greenhouse Gas Inventory – Buildings.” Sustainability Office and Facilities and Services at the University of Toronto, [online article], (February 2007), available at: <www.sustainability.utoronto.ca>
- ↑ U.S. Department of Energy, “Review of Combined Heat and Power Technologies,” [online article], (October 1999), available at: <www.eere.energy.gov/de/publications.html>
- ↑ "HFCIT Fuel Cells: Types of Fuel Cells." Energy Efficiency and Renewable Energy. U.S. Department of Energy. [online article], available at: <www1.eere.energy.gov/hydrogenandfuelcells/fuelcells/fc_types.htm >.
- ↑ Krist, Kevin. "Solid Oxide Fuel Cell Residential Cogeneration." Fuel Cell Technology Review Conference. [online article], available at: <www.netl.doe.gov/publications/proceedings/99/99fuelcell/fc4-2.pdf>.
- ↑ De Guire, Eileen J, “Solid Oxide Fuel Cells” Review Article. [online article] (Released April 2003), available at:<www.csa.com/discoveryguides/fuecel/overview.php>
- ↑ Talbot, David, “A Practical Fuel-Cell Power Plant” [online article] (October 23, 2006) available at: <www.technologyreview.com/Energy/17644/>
- ↑ Hart, Nigel, N.P. Brandon, M.H. Day, and J.E. Shemilt. Environment Impact of Fuel Cell Manufacturing. Ed. Augustin J. McEvoy. Proceedings of the 4th European Solid Oxide Fuel Cell Forum, July 2000. Switzerland: European Fuel Cell Forum, 2000.
- ↑ Teagan , W. Peter, Jan H.J.S. Thijssen, Eric J. Carlson, and Carole J. Read. Current and Future Cost Structures of Fuel Cell Technology Alternative. Ed. Augustin J. McEvoy. Proceedings of the 4th European Solid Oxide Fuel Cell Forum, July 2000. Switzerland: European Fuel Cell Forum, 2000.
- ↑ “SECA Fuel Cell Development Program Completes Phase I”, National Energy Technology Laboratory [online article], available at: <www.netl.doe.gov>
- ↑ “University of Toronto Budget Report 2005-2006” [online document], available at: <www.utoronto.ca/planning/budget/>
- ↑ Nassim, Liza, Dean of Students Woodsworth College, Personal Communication. February 1, 2008.
- ↑ Graedel, Thomas E, Streamlined Life-Cycle Assessment, New Jersey: Prentice Hall, 1998.
- ↑ 14.0 14.1 Boon Teak Lee, Chief Engineer of U of T Central Steam Plant, Personal Communication, February 4, 2008.
- ↑ Ontario Power Generation, “2006 Annual Report,” [online article], available at: <www.opg.com/pdf/annual%20reports/annual%20report%202006.pdf>
- ↑ Energy Information Administration, “Natural Gas Weekly Update,” [online article], (February 28 2008), available at: <tonto.eia.doe.gov/oog/info/ngw/ngupdate.asp>
- ↑ EIA National Energy Information Center, “Natural Gas 1998: Issues and Trends,” [online article], (1998), available at: http://www.eia.doe.gov/oil_gas/natural_gas/analysis_publications/natural_gas_1998_issues_and_trends/it98.html.
- ↑ Saskatchewan Waste Reduction Council, “Recycling Steel,” [online article], (1998), available at: http://www.saskwastereduction.ca/metal/steel.html.
- ↑ Boon Teak Lee, Chief Engineer of U of T Central Steam Plant, Personal Communication, February 4, 2008.
- ↑ Manturbo, “Cogeneration Plant,” [online article], (2001), available at: www.manturbo.com/bin/startdownloadbycms.php?ChannelType=turbinen&ID=46&FieldName=EN_File.
- ↑ American Academy of Otarlyngology-Head and Neck Surgery, “Noise and Hearing Protection,” [online article], (2008), available at: http://www.entnet.org/healthinfo/hearing/noise_hearing.cfm.
- ↑ Thomson, MIE 315 Design for the Environment Class Notes, University of Toronto (2008).